Chemical Looping Combustion
Chemical looping combustion (CLC) is an innovative technology for producing energy from fuels while inherently separating the resulting CO2 into a nearly-pure stream for subsequent permanent storage or utilization. Unlike post-combustion CO2 separation from flue gases or production of pure oxygen needed for gasification or oxy-fuel combustion, both of which are expensive and very energy-intensive, CLC uses the natural reversible oxidizability of metals to separate oxygen from air with almost no additional energy. CLC is still on the path towards commercialization and no full-scale plants are operating today, but thanks to global R&D efforts and an inspired community of researchers, the technology is maturing.
The most common implementation of CLC is to circulate sand-like particles that contain a metal such as nickel, iron or copper between two fluidized bed reactors. One reactor is fluidized with air, which oxidizes the metal in the particles. The particles are then separated from the fluidizing gas, carrying the oxygen with them and effectively separating oxygen from the air. The particles flow into the other reactor, into which fuel is fed and reacts (combusts) with the oxygen on the particles. The resulting product gases are primarily CO2 and H2O, and once the water is condensed out, a nearly-pure CO2 stream results. An important aspect of chemical looping that drives overall performance of the system is the "oxygen carrier" particles. They must be capable of withstanding high temperatures, have high oxygen transport capacity, take up and release oxygen quickly, retain activity for thousands of cycles, and be physically robust, readily available and affordable.
Chemical Looping R&D at the University of Utah
We have been researching CLC since 2007. Mostly, we have focused on a variant of CLC known as Chemical Looping with Oxygen Uncoupling (CLOU), which involves use of an oxygen carrier that spontaneously liberates gaseous O2 in the fuel reactor. The value of this is that the O2 reacts readily with solid fuel such as coal char. In conventional (non-CLOU) CLC, the char must first be gasified in-situ by steam to make H2 and CO, which can then react heterogeneously with oxygen in the carrier material. We have primarily studied the CuO/Cu2O system, starting with fundamental studies to understand reaction kinetics, progressing into oxygen carrier development and fluidized bed reactor studies. We have constructed two continuous dual fluidized bed systems, a 10 kWth electrically heated system with bubbling beds and a 220 kWth process development unit (PDU) that processes 0.5 to 1 ton/day of fuel, depending on the type.
In recent years, we have expanded our focus to include chemical looping of agricultural and forest waste, as well as the combustible portion of municipal solid waste, in order to efficiently achieve negative CO2 emissions. We are achieving first-of-a-kind tests of chemical looping in the PDU system.
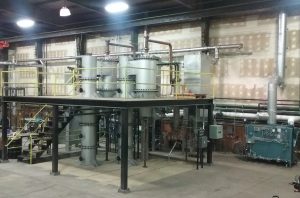
220 kW chemical looping combustion process development unit (PDU)
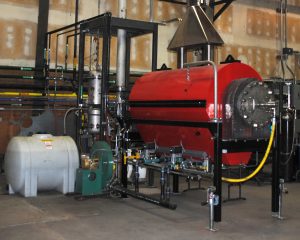
Rotary kiln used for large-scale production of chemical looping oxygen carrier materials.